Fuel For Thought
Fuel For Thought
An emergency generator and its associated fuel system need to be ready to go during a commercial power outage. That’s exactly why it was installed in the first place. For many businesses such as telecommunications, data centres, and healthcare facilities, a building power failure is not an option and can be devastating. Power outages can lead to fines, customer dissatisfaction, and even loss of lives.
These businesses can spend millions of pounds in designing and constructing their emergency backup generator systems. However, after Installation ends, they don’t always invest similarly later in Preventative maintenance of systems. Even when they do, they might overlook a crucial component of the emergency generator system. It can be easy to lose perspective that everything begins with the fuel, and the quality of that fuel is extremely important.
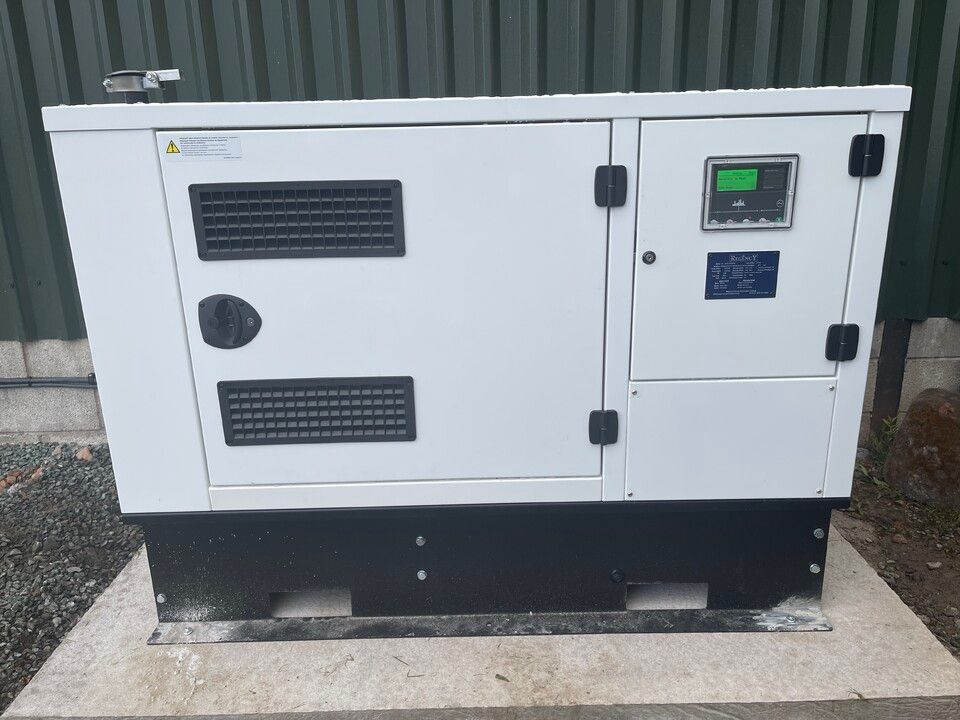
Why are fuel sampling and testing necessary?
In an emergency generator fuel system when seldom used, the fuel can stay stagnant for several years or even decades. Since diesel fuel is a refined oil product (Hydrocarbon), it will ultimately naturally begin to break down into its pre-refined self in as little as 6 months. This degradation is much more accelerated than it used to be.
As the fuel breaks down, there can be solid byproducts that lead to sediment and particulates within the fuel tank. In addition, since fuel is a hydrocarbon, water is naturally integrated into its chemical makeup. Over time, the water can separate out from the fuel or condensation and debris can be introduced into your tank from the outside via vents or other means. Water in your fuel tank contributes to the oxidation of metal components as well as bacterial and fungal growth (microbes). If your emergency generator fuel system hasn’t had proper fuel testing and maintenance, it might not be ready to perform in those critical moments of need.
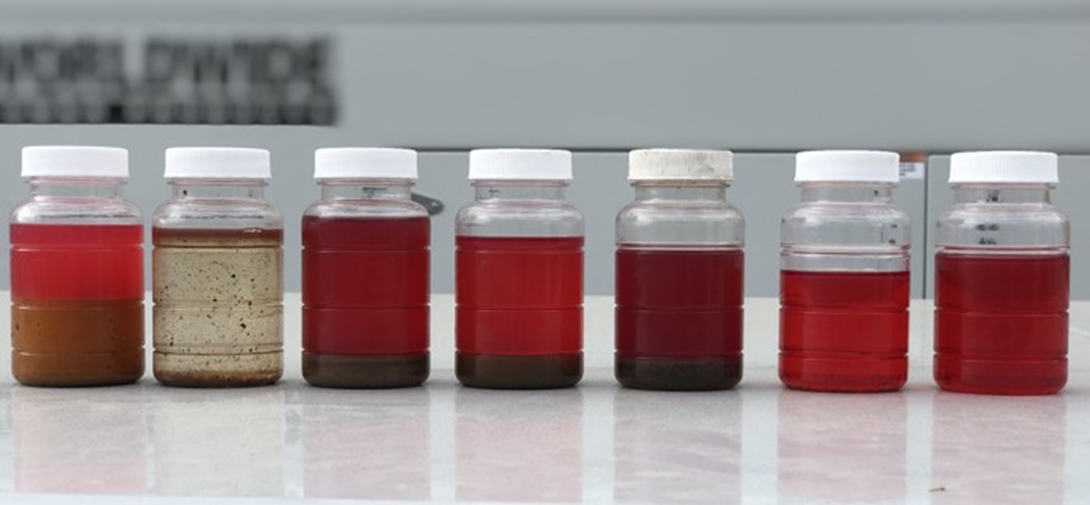
What happens when fuel quality is ignored?
All of these factors may not seem very problematic at first glance, but they lead to serious fuel quality problems. Sediment and sludge can clog filters, damage pumps, and lead to generator loss of prime and ultimate failure. Water contributes to microbial growth and microbes and their particulates can clog filters and microbe excrements lead to corrosion of steel fuel tanks, piping, and/ or pumping equipment. Fuel quality problems like these lead to emergency generator failure.
How can fuel quality problems be prevented?
Emergency generator owners must have a solid preventative maintenance program that includes a routine sampling of their fuel tanks. They need to have a professional who knows what they are doing and is consistent during each sampling event. Fuel samples need to be collected in a fashion that represents the fuel that is picked up by the pumps feeding the generator or smaller holding tanks (day tanks). Often there is no reason to pull a sample from the very tank bottom or from generator fuel filters except to generally observe them.
Why would we send a sample from the tank bottom that is half full of water only for the lab to tell us there is water in your fuel? We already know there is a problem if the fuel sample has visual evidence of water, therefore the collection of a representative sample from above the water line and sending that for laboratory analysis is generally a better practice and more useful in designing or enhancing the overall fuel treatment action plan.
Fuel samples need to be collected consistently and in a fashion that represents the fuel that is picked up by the pumps feeding your generator or smaller holding tanks (day tanks). A fuel sample collected from the very bottom of your fuel tank, although useful for visual analysis, isn't the sample you necessarily send off for laboratory analysis.
Likewise, a fuel sample collected upstream from generator fuel filters will not represent what is happening inside the fuel tank near your tank's draw (pickup) point. Instead, the sample should be pulled from an interval that best represents where fuel is drawn from your tank. This interval can undoubtedly vary, but it is generally between 1" and 6" from the tank bottom. The actual draw point can be verified via fuel system drawings, interior inspection reports, or other means. CFCS generally collect representative fuel samples from 4" -6" off the tank bottom when the draw point is unknown, which is the case most of the time.
Also, if water is already present in the tank bottom, we will collect the sample a minimum of 2" higher than the water level. Remember, we want to get analytical results on the fuel, not the water. Suppose there is water on the tank bottom. In that case, there is already a problem to remedy, so use your sample budget to understand the fuel quality better so you can add the proper treatment into your work plan to fix the water problem.
How do we collect a fuel sample from a particular fuel level without cross-contaminating it with other fuel in the tank?
Sampling devices known as "bacon bombs" can help you achieve this goal. They remain closed and empty until you reach the level you want, then open to capture fuel and closed before extracting them from your fuel tank. Another way to extract the sample is by using a hand pump and tubing with some finesse at the levels from which you want to collect.
We are often asked, "what is a comprehensive fuel analysis"?
Opinions may vary throughout the industry and can also become very situational. Several types of fuel analysis can provide you with detail ranging from general fuel quality to much more detailed analysis, such as proving a fuel's specifications. Striking an economical balance is the key for an entry-level comprehensive analysis suite and might contain the following breakdown:
- Iso 4406 Cleanliness to IP630 A
- Bio % F.A.M.E To ASTM D8274
- Density to ASTM D7777
- Cetane to ASTM D613
- Clear & Bright to ASTM D4176
- Visual inspection
- Biological Activity = ATP
- Flash Point to ASTM D975
- PPM Moisture to ASTM D6304
- Cloud Point to ASTM D7397 (identifies S/W grade)
- FBT (Filter blocking tendency) IP 387 Procedure B
- Viscosity (ASTM D7042)
Contact cfcs@contaminatedfuel.co.uk to discuss your requirements on fuel and oil analysis.
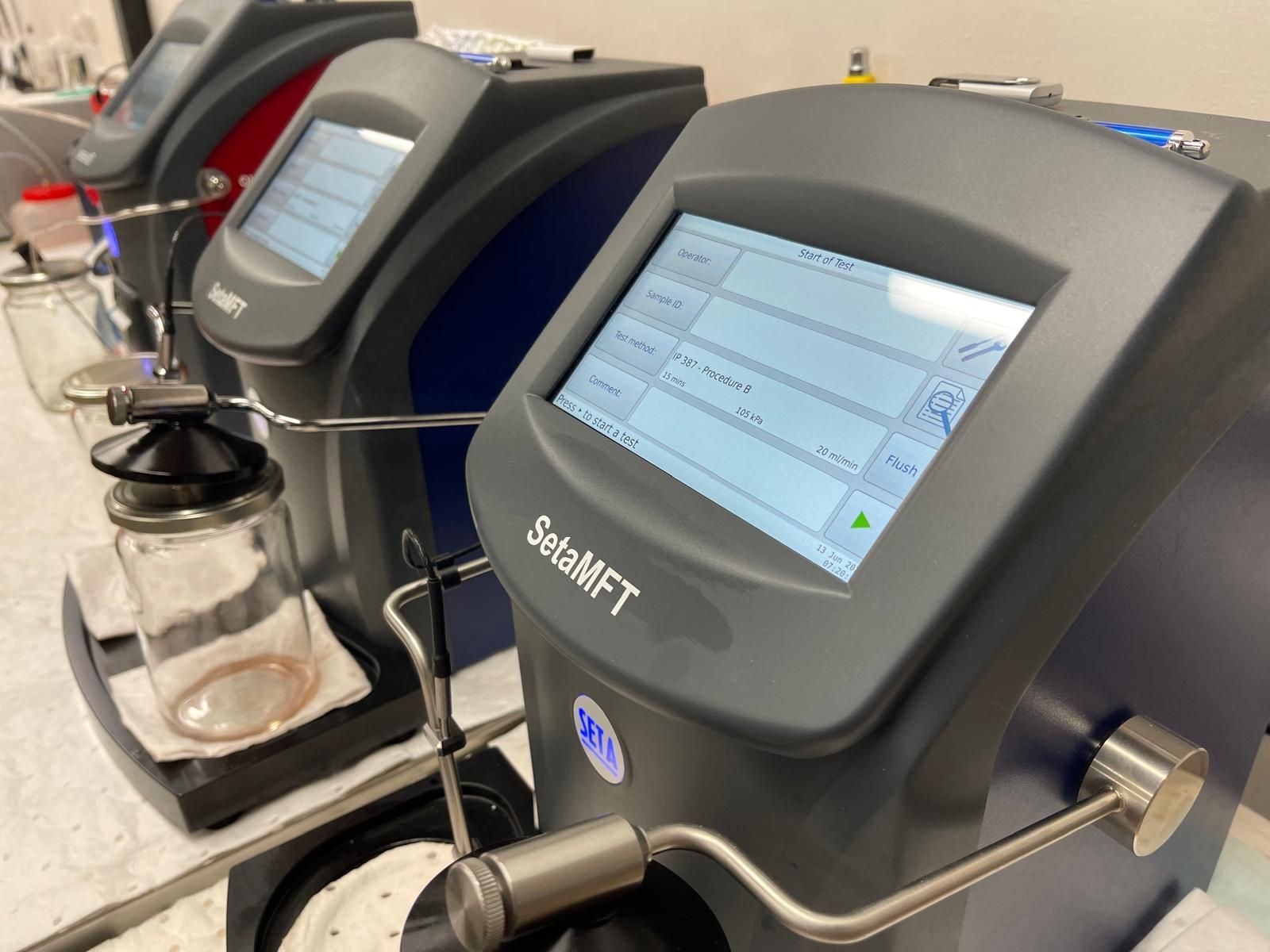